Comparing Weld-On and Bolt-On Hinges: Key Performance Differences and Ideal Uses

Hinges are fundamental components for doors, windows, and equipment enclosures, forming a massive global market. According to Grand View Research (2024), the global door hinge market size was valued at approximately $9.5 billion in 2024 and is expected to grow steadily in the coming years.
By installation method, hinges are primarily categorized into:
- Weld-On Hinges: Permanently fused to the frame and door via welding.
- Bolt-On Hinges (also known as Screw-On or Standard Hinges): Installed using screws or bolts, allowing disassembly.
As durability and security become increasingly important, weld-on hinges are emerging as the preferred choice for heavy-duty, tamper-resistant applications.
Terminology and Hinge Types
Weld-On Hinges
- Installed via welding (MIG, TIG, Stick)
- Provide a permanent, non-removable bond
- Common materials: 304/316L stainless steel, forged alloy steel
- Examples: Barrel hinges, bullet hinges, pintle hinges
Bolt-On Hinges
- Attached using screws or bolts
- Allow for easy disassembly and replacement
- Variants include:
- Light-duty (residential): e.g., 2 Ball Bearing (2BB) hinges
- Medium-duty (commercial): 4BB hinges
- Heavy-duty (industrial): roller bearing or thick-leaf designs
Structural Differences
Load Path Efficiency
- Weld-on hinges transfer load directly through welded joints—more uniform stress distribution and less movement.
- Bolt-on hinges distribute load across multiple fasteners and interfaces—higher risk of play or failure under stress.
Material Thickness
- Weld-on: Often ≥ 6 mm thick; stronger under shear and torsion
- Bolt-on: Typically 2–5 mm thick; suitable for lighter loads
Pin Configuration
- Weld-on hinges often use non-removable pins for anti-tamper design
- Bolt-on hinges typically feature removable pins for maintenance
Mechanical Performance: Load, Fatigue, Impact
Static Load Capacity
- Weld-on hinges withstand significantly more torque and radial load without deformation.
- Bolt-on hinges may experience screw pull-out under similar forces.
Fatigue Life (Cycle Durability)
- Welded joints eliminate play—enabling 500,000+ cycles without failure.
- Bolt-on types may require re-tightening or component replacement after 50,000–100,000 cycles.
Impact Resistance
- Weld-on models spread impact forces into the structure—ideal for high-shock applications.
- Bolt-on hinges may fail at screw holes under sudden impact loads.
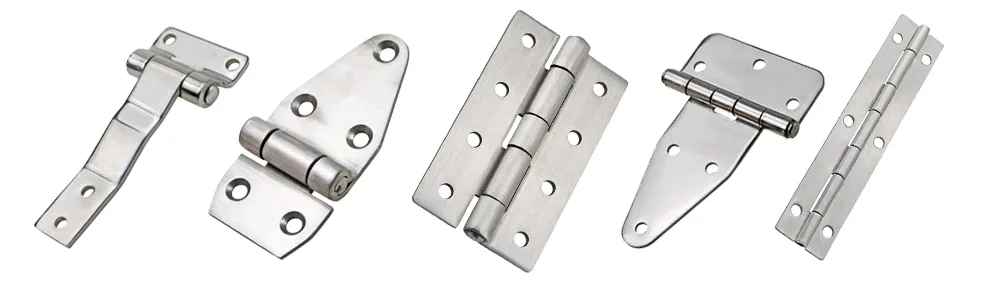
Installation Process Comparison
Weld-On Hinge Installation
- Requires surface cleaning, positioning, tack weld, full weld, grinding, and finishing
- Tools: Welder (TIG/MIG), clamps, grinders
- Average time per hinge: 10–20 minutes (skilled welder)
Bolt-On Hinge Installation
- Involves marking, drilling, screwing, and alignment
- Tools: Drill, driver, level
- Average time per hinge: 3–5 minutes
Removability
- Weld-on hinges: Permanent; removal requires cutting
- Bolt-on hinges: Easily disassembled; parts reusable
Corrosion Resistance & Environmental Suitability
Material Choices
- Weld-on hinges: 304/316L stainless steel or hot-dip galvanized steel
- Bolt-on hinges: Often plated or powder-coated steel
Salt Spray Test (ASTM B117)
- 316L stainless weld-on: 1,000+ hours corrosion resistance
- Zinc-plated bolt-on: May show corrosion after 100–300 hours
Temperature Extremes
- Welded joints maintain strength under high heat; may need post-weld heat treatment
- Bolt-on hinges risk fastener loosening and lubricant failure at extreme temperatures
Maintenance and Lifecycle Cost Analysis
Maintenance Frequency
- Weld-on hinges: Virtually maintenance-free post-installation
- Bolt-on hinges: Require periodic bolt tightening, pin lubrication, and cleaning
Common Failure Modes
- Weld-on: Weld fatigue or base metal cracking
- Bolt-on: Loose fasteners, worn bearings, stripped threads
Total Cost of Ownership (TCO)
- Weld-on: Higher upfront cost; lower lifetime maintenance
- Bolt-on: Lower initial cost; higher cumulative maintenance over 10+ years
Security and Vandal Resistance
Anti-Intrusion Design
- Weld-on: No removable parts; ideal for high-security applications
- Bolt-on: Exposed fasteners present potential attack points
Fire Resistance
- Steel weld-on hinges maintain strength near 800°C+
- Bolt-on hinges may fail as screws lose tension under heat
Common Application Scenarios
Application Type | Recommended Hinge | Reason |
---|---|---|
Industrial Equipment | Weld-On Hinges | Shock, vibration, no maintenance |
Residential Gates | Bolt-On Hinges | Style flexibility, easy adjustments |
Refrigerated Trucks | Hybrid (Weld-On + Bolt-On) | Heavy-duty + serviceable access |
Hinge Selection Guide (Decision Matrix)
Requirement | Best Option |
---|---|
Heavy Load (>500 kg) | Weld-On |
Frequent Maintenance | Bolt-On |
Marine/Corrosive Environment | Weld-On (316L SS) |
High-Security Needs | Weld-On |
Low Initial Budget | Bolt-On |
Conclusion
Weld-on hinges are the go-to solution for extreme environments, security-sensitive applications, and long-life industrial installations. Their robust structure, low maintenance needs, and superior fatigue life make them ideal for:
- Machinery doors
- Detention facilities
- Marine/offshore applications
Bolt-on hinges are best suited for:
- Light-to-medium duty access panels
- Projects requiring disassembly or style changes
- Budget-conscious installations
Optimal Strategy: Combine Both
Use weld-on hinges for main access and bolt-on hinges for secondary doors or removable panels. This hybrid approach ensures safety, performance, and maintainability across applications.